Background of Metal Hose Production
Metal Braided Hoses are an essential component of modern industrial piping systems. Thanks to their excellent flexibility, fatigue resistance, high-pressure tolerance, resistance to extreme temperatures, and corrosion resistance, they are widely used in industries such as aerospace, petrochemicals, mining electronics, machinery manufacturing, shipbuilding, healthcare, textiles, energy, and construction. In various gas and liquid transportation systems, as well as in systems requiring compensation for length, temperature, position, and angle, metal braided hoses are commonly employed as compensation components, sealing components, connection components, and vibration-damping components.
But here’s the catch: welding metal braided hoses can be tricky. If not done properly, weak welds can lead to leaks, failures, and expensive rework. That’s why more manufacturers are shifting to automated TIG welding for better precision and reliability.
Let’s break it down—what makes metal braided hose welding challenging, and how can automation make a huge difference?
The Structure of Metal Braided Hoses
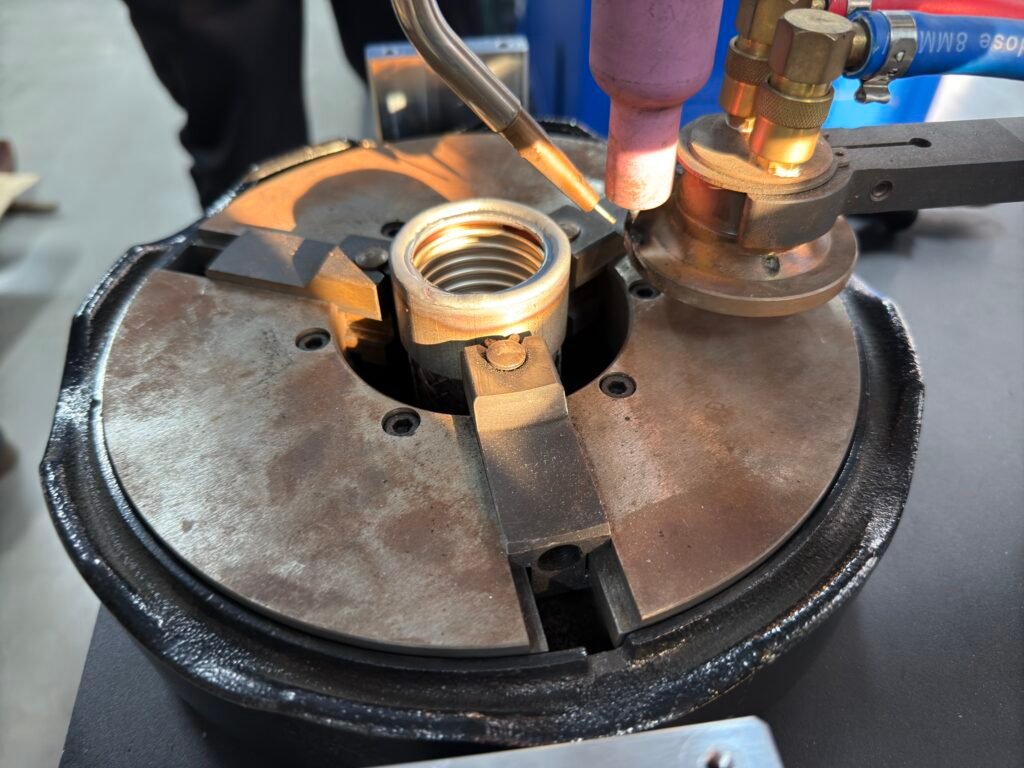
Metal braided hoses typically consist of three main components:
- Corrugated Tube – This is the core of the hose, providing flexibility and strength. It has a thin wall and is inherently elastic.
- Braided Layer – Made of stainless steel wires or bands, this adds reinforcement to handle high pressure.
- Neck Ring – This secures the braided layer in place and helps with assembly.
When assembling these parts, manufacturers typically weld them together before attaching fittings such as flanges, threaded joints, or quick connectors. And this is where things can get complicated.
The Welding Challenge – Irregular Gaps and Precision Demands
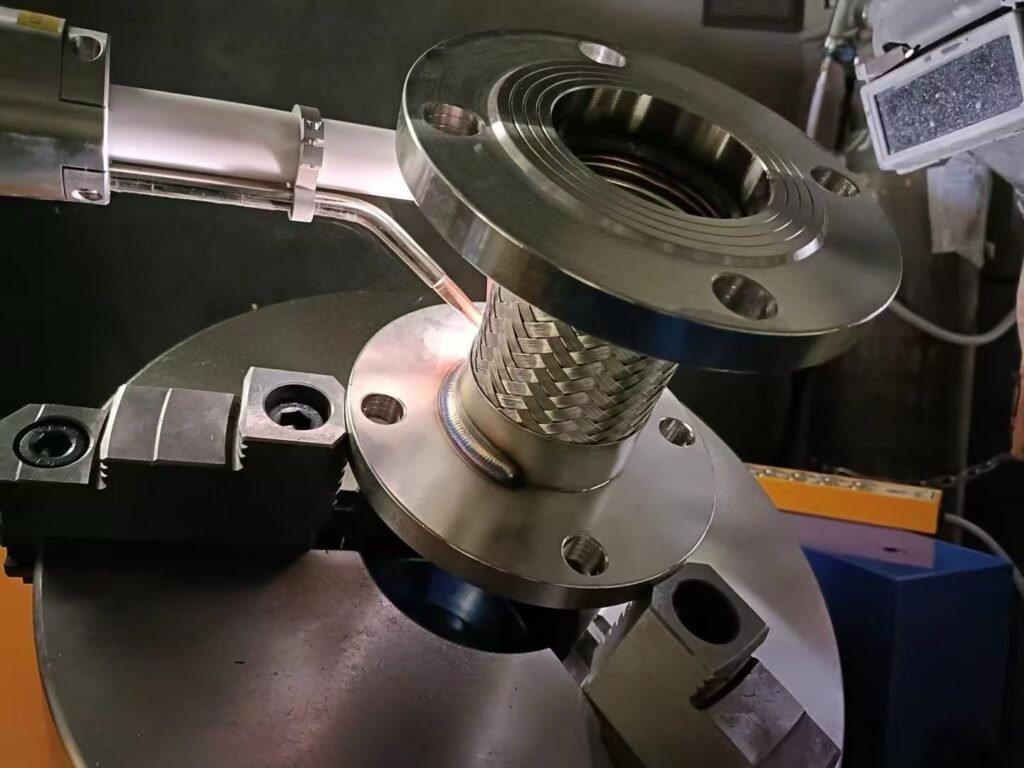
Welding metal braided hoses isn’t as simple as joining two solid pieces of metal. The main challenges include:
- Irregular Gaps – The braided layer doesn’t sit perfectly flush with the corrugated tube, creating uneven gaps.
- Thin-Walled Materials – The core tube’s thin structure makes it prone to burning through if the welding heat isn’t controlled.
- Tight Space Constraints – Welding the assembly together, especially with the circular seam, requires high precision to avoid defects.
Traditionally, these challenges have been tackled through manual TIG welding, but let’s be real—manual welding has its limits.
The Drawbacks of Manual Welding
1. Inconsistent Quality
Every welder has their own technique, which means every weld is slightly different. Some are perfect, while others might have slight porosity, cracks, or weak penetration. This inconsistency can be a real headache when dealing with high-pressure hoses.
2. Slow and Labor-Intensive
Welding metal braided hoses manually takes time, and when production volumes are high, manual welding slows things down significantly. Plus, the longer a welder works, the higher the chance of fatigue-related errors.
3. High Rework and Scrap Rates
Even skilled welders make mistakes, and with such delicate welding work, defects happen. This results in costly rework, wasted materials, and potential delays in production.
4. Operator Fatigue and Safety Concerns
Holding steady and focusing on precise TIG welding for extended periods is exhausting. Fatigue leads to shaky hands, inconsistent heat control, and higher defect rates—not to mention the physical toll on welders over time.
The Game-Changer: Automated TIG Welding for Metal Braided Hoses
Automation has revolutionized metal hose welding. Here’s why more manufacturers are making the switch to automated TIG welding solutions:
✅ Precision & Consistency
Automatic TIG welding ensures uniform penetration and flawless welds every single time. The machine follows programmed parameters, eliminating human error and variations in quality.
✅ Increased Productivity
Instead of manually welding one piece at a time, automated systems can continuously process multiple hoses with speed and efficiency, drastically increasing output.
✅ Stronger, Leak-Proof Welds
Advanced control over welding speed, current, and arc ensures deep penetration without overheating. This leads to superior weld strength, which is essential for high-pressure and high-temperature applications.
✅ Reduced Costs and Waste
Since automated systems minimize defects, manufacturers save on material waste, rework costs, and labor expenses. Over time, this translates to a significant return on investment.
Key Welding Steps in Metal Braided Hose Manufacturing
1. Braided Layer Sealing Welding
After the stainless steel braid is applied over the corrugated tube, it needs to be securely sealed to prevent fraying and maintain structural integrity. This weld must be precise—too much heat can damage the thin-walled tube, while too little results in a weak seal. Automated TIG welding machines handle this process with pinpoint accuracy, ensuring a strong, uniform bond.
2. Circumferential Welding of End Fittings
To connect metal braided hoses to external systems, end fittings like flanges, threaded joints, or quick connectors must be welded onto the hose ends. This circumferential (ring) welding needs to be completely leak-proof and strong enough to withstand high pressure and dynamic stress. Automated welding systems guarantee perfect alignment and optimal penetration, making them ideal for this critical step.
Why Automatic Welding Machine for Metal Hose Matters
Some of our clients from developed countries have shared feedback with us: experienced welding workers are extremely expensive. Investing in automatic welding machines is far more cost-effective than relying on manual welding. Additionally, the welding quality achieved by machines is consistently high. In contrast, even the most skilled welders often struggle to maintain consistency with manual welding. Issues such as small leaks and uneven welds are common, leading to a high rate of rejected parts.
China has a large base of heavy industrial needs, which is why the country has almost fully upgraded to TIG automatic welding machines. This shift has given China a competitive advantage in exporting metal hoses and related products, allowing them to offer lower prices while delivering superior welding quality.
The best part? Manufacturers using automatic welding solutions save money in the long run by reducing waste and significantly improving efficiency.
Stay Competitive with Automated Welding
The demand for stainless steel flexible hoses is only growing, especially in industries like oil & gas, chemical processing, and HVAC systems. To stay ahead of the competition, manufacturers need reliable, cost-effective welding solutions that guarantee top-quality products.
If you’re still relying on manual TIG welding for your metal braided hose production, it might be time to explore automation. The right automated TIG welding machine can revolutionize your process, boost productivity, and improve product quality—without the headaches of manual welding.
Upgrade Your Welding Process Today
Interested in learning how automated welding can improve your metal braided hose production? Contact us today to explore our range of automated TIG welding solutions!