The expansion joint industry plays a crucial role in maintaining the integrity and flexibility of piping systems in various sectors, from power plants to petrochemical facilities. The need for reliable, high-quality welds in the fabrication of expansion joints has driven the adoption of advanced welding techniques, particularly TIG (Tungsten Inert Gas) welding. While MIG (Metal Inert Gas) welding is also widely used, TIG welding has become the preferred choice for achieving superior precision and cleanliness in expansion joint manufacturing.
TIG/MIG Welding in the Expansion Joint Industry
Both TIG and MIG welding processes have distinct advantages, making them suitable for different aspects of expansion joint production:
- TIG Welding:
TIG welding is renowned for producing high-quality, precise, and clean welds. It uses a non-consumable tungsten electrode and an inert gas shield (typically argon) to protect the weld pool, making it ideal for thin-walled materials like those commonly used in the production of expansion joints. TIG welding is especially effective for critical joints that require minimal distortion and maximum strength, such as those found in pressure vessels and metal hoses. This makes it the preferred method for high-precision, high-strength welding applications in the expansion joint sector. - MIG Welding:
MIG welding, on the other hand, uses a consumable wire electrode and is typically faster than TIG welding. It is often used in applications where speed is prioritized over absolute precision, and while it can be effective for thicker materials, it doesn’t offer the same level of control or clean finish that TIG welding provides. In expansion joint fabrication, MIG is usually applied to large-scale manufacturing or less critical welds, where a balance between speed and quality is necessary.

Manual TIG vs. Fully Automated TIG Welding in Expansion Joint Manufacturing
While manual TIG welding has been the industry standard for years, advancements in automation are rapidly transforming the welding process, particularly in the expansion joint sector. Here’s a closer look at the two methods:
Manual TIG Welding:
Advantages:
- Flexibility in handling a wide range of joint configurations and sizes.
- Ideal for small production runs or custom, high-precision parts.
- Skilled welders can make adjustments in real-time to correct defects or variations in the material.
Disadvantages:
- Labor-intensive, requiring highly skilled welders with significant training and experience.
- Prone to human error, leading to inconsistent welds, particularly in complex or repetitive applications.
- Slower production speed, increasing costs for larger runs.
Fully Automated TIG Welding:
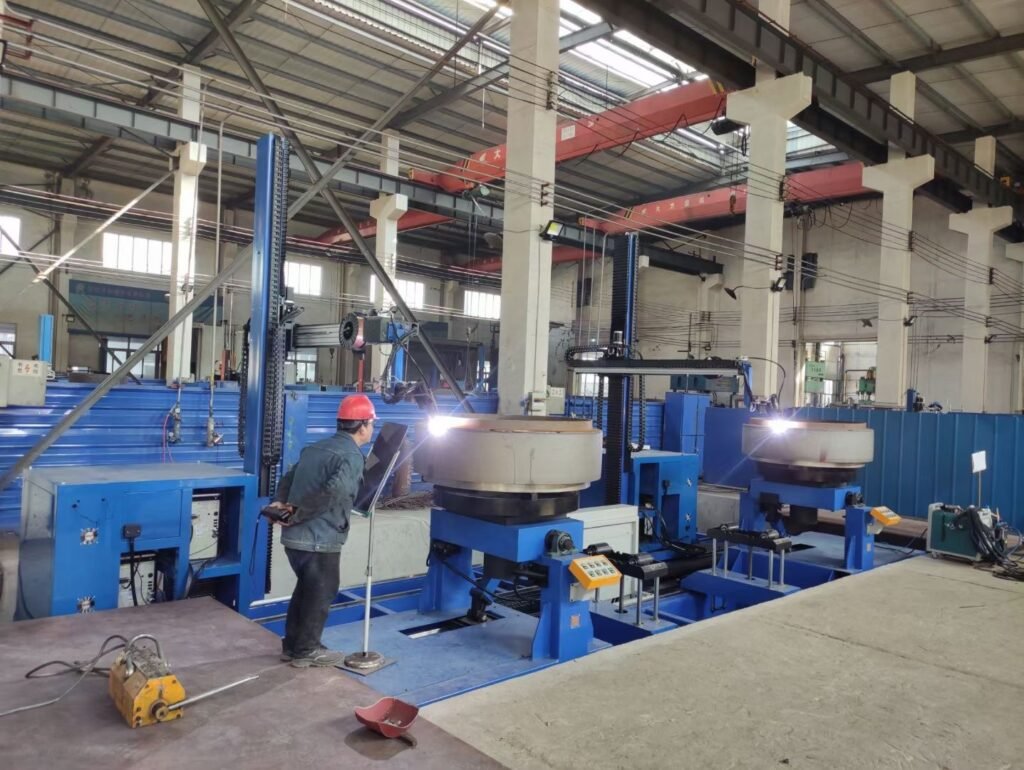
Advantages:
- Consistency and Precision: Automated TIG welding systems can perform repetitive tasks with unmatched precision, ensuring high-quality welds every time.
- Increased Productivity: Automated systems can work continuously, significantly reducing welding time and boosting throughput.
- Reduced Labor Costs: By eliminating the need for manual labor, automated systems reduce the risk of errors and lower operational costs over time.
Disadvantages:
- Initial Investment: Automated welding equipment requires a higher initial investment compared to manual methods.
- Customization: While automated systems excel at repetitive tasks, they may require adjustments for highly customized or intricate projects.
The Trend Toward Automation in the Expansion Joint Industry
The trend in the expansion joint industry is clear: automation is the future. As demand for faster production, higher precision, and lower operational costs increases, more manufacturers are turning to fully automated welding systems.
Key Benefits Driving the Trend:
- Higher Demand for Consistency: In industries like oil and gas, power generation, and aerospace, expansion joints need to meet stringent quality standards. Automated TIG welding ensures consistent welds, which is crucial for the safety and reliability of the systems.
- Increased Production Speed: Automation can significantly reduce production time, allowing manufacturers to meet the growing demand for expansion joints without compromising quality.
- Reduced Reliance on Skilled Labor: The shortage of highly skilled welders is a concern in many countries, making automated welding solutions an attractive alternative. By shifting to automation, manufacturers can reduce their dependence on labor while still achieving high-quality results.
- Customization and Flexibility: Advanced robotic systems and automated welding machines can be programmed to handle a variety of joint sizes and configurations, offering manufacturers both the flexibility to produce custom expansion joints and the efficiency of automation for large runs.
Conclusion: The Future of Welding in Expansion Joints
As the expansion joint industry continues to evolve, TIG welding will remain at the heart of high-precision applications, especially when combined with the efficiency and reliability of automation. With fully automated TIG welding systems on the rise, manufacturers can achieve unparalleled consistency, speed, and cost savings, meeting the ever-increasing demands of the industry.
At the same time, manual TIG welding will still have its place in highly customized or low-volume production environments, where flexibility and hands-on adjustments are essential.
Ultimately, the future of expansion joint manufacturing lies in the seamless integration of automated systems that combine the precision of TIG welding with the advantages of automation, creating a new standard of quality and efficiency.